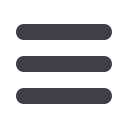
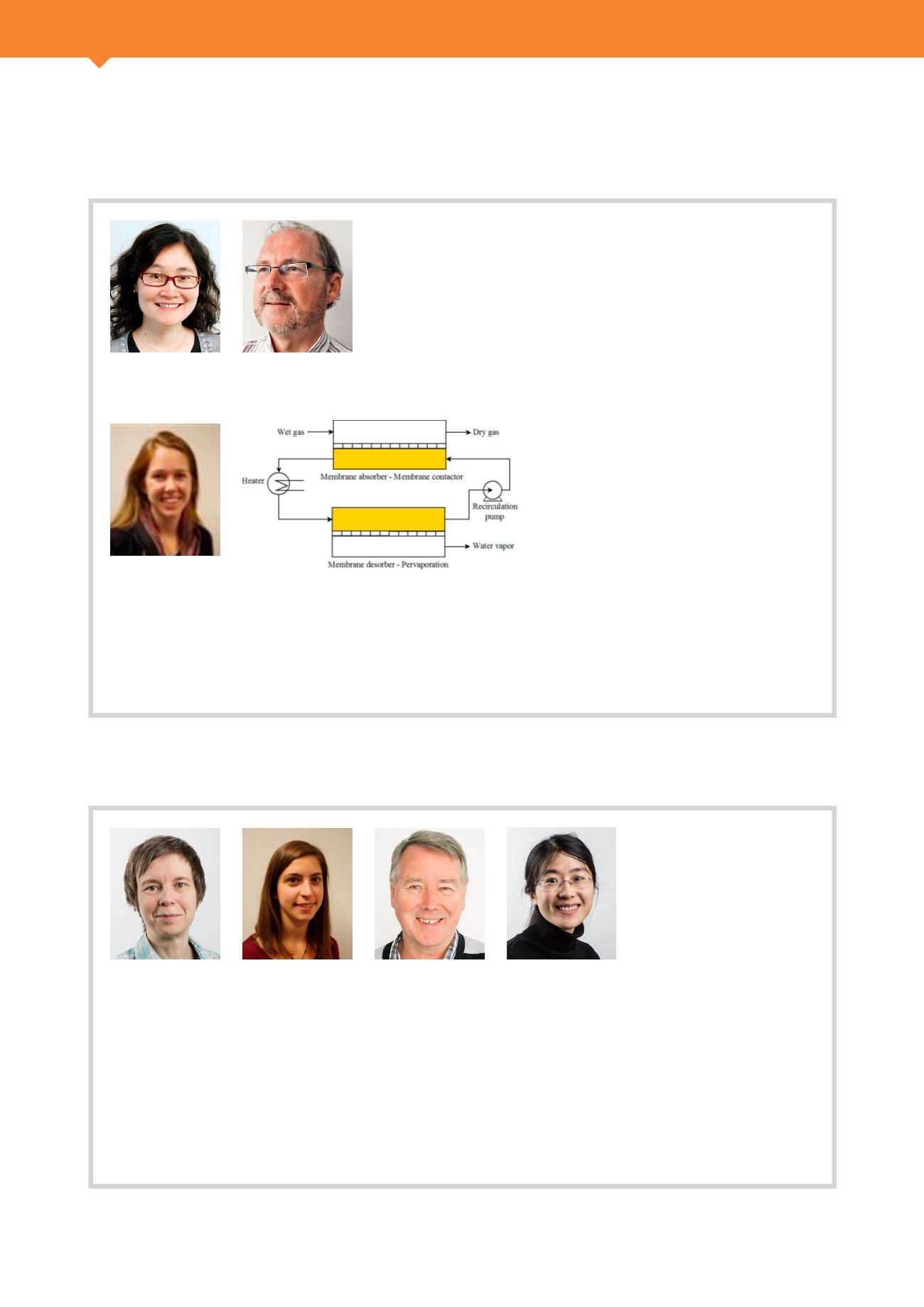
16
SUBPRO Subsea Production and Processing
used for hydrate control in the
well flowlines, giving in total 3
different chemical systems with
separate absorption and regen-
eration equipment. Simplifying
the chemical systems or mov-
ing equipment and process ele-
ments subsea could be a way to
ensure better energy efficiency
and utilization of the resources.
The objective of this project is to develop a
regenerative process where hydrate formation is
controlled and H
2
S is removed. Since this would
be a regenerative process, significantly higher
concentrations of H
2
S could be treated than what
normally is the case with e.g. triazine. The work will
contain both modelling and experimental studies.
Pipelines used to transport produced gas have
quality restrictions related to content of water, CO
2
,
H
2
S and heavy hydrocarbons. If these requirements
cannot be met by the well flow, separation is re-
quired either topside or subsea. Today on a typical
platform, water is removed by Triethylene glycol
while CO
2
and H
2
S is removed by amine processes.
In addition to this, Mono-ethylene glycol (MEG) is
H
2
S and hydrate control, particle breakup/contactor studies
Project manager and PhD
supervisor, Associate
Prof. Hanna Knuutila
PhD candidate, Eirini
Skylogianni
Postdoc, Jing Shi
One of the main process-
ing steps in natural gas
processing is dehydration.
This has been identified by
our industry partners as a
major challenge, in order
to prevent hydrate for-
mation, slug flow, corro-
sion and erosion in pipes
and process equipment.
Membranes for gas dehydration
Project manager and main
PhD supervisor, Associate
Prof. Liyuan Deng
PhD candidate,
Kristin Dalane
Co-supervisor, Prof.
Magne Hillestad
The objective for this project is to evaluate a new
membrane process design for subsea natural gas
dehydration
(Figure 13)
to reach pipeline transport
specifications. To evaluate the membrane dehy-
dration process, modelling and process simula-
tion will be conducted. The two membrane mod-
ules will be modelled and verified before they are
implemented into the simulation tool HYSYS for
an overall process design evaluation and optimi-
zation. With a verified and optimized process sim-
ulation model a feasibility study of the membrane
dehydration process can be reported. In a later
stage, there will be a need for verification of mod-
els through experimental testing.
With subsea dehydration, no water will be present
in downstream gas pipelines and process equip-
ment, which gives several advantages: Prob-
lems connected to
multiphase transport will be
removed and there is no need for other mitigation
techniques as continuous injection of preven-
tion chemicals like Mono-ethylene glycol (MEG).
In addition, dehydration in an earlier processing
stage will reduce the cost and complexity of the
downstream equipment.
Figure 13. Preliminary process design for closed
loop membrane dehydration with glycol. Water from
wet natural gas is absorbed by glycol in a membrane
contactor, and glycol is regenerated with pervapora-
tion where the water is removed from the rich glycol.
Co-supervisor, Prof. Emeritus
Hallvard Fjøsne Svendsen