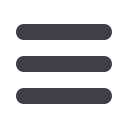
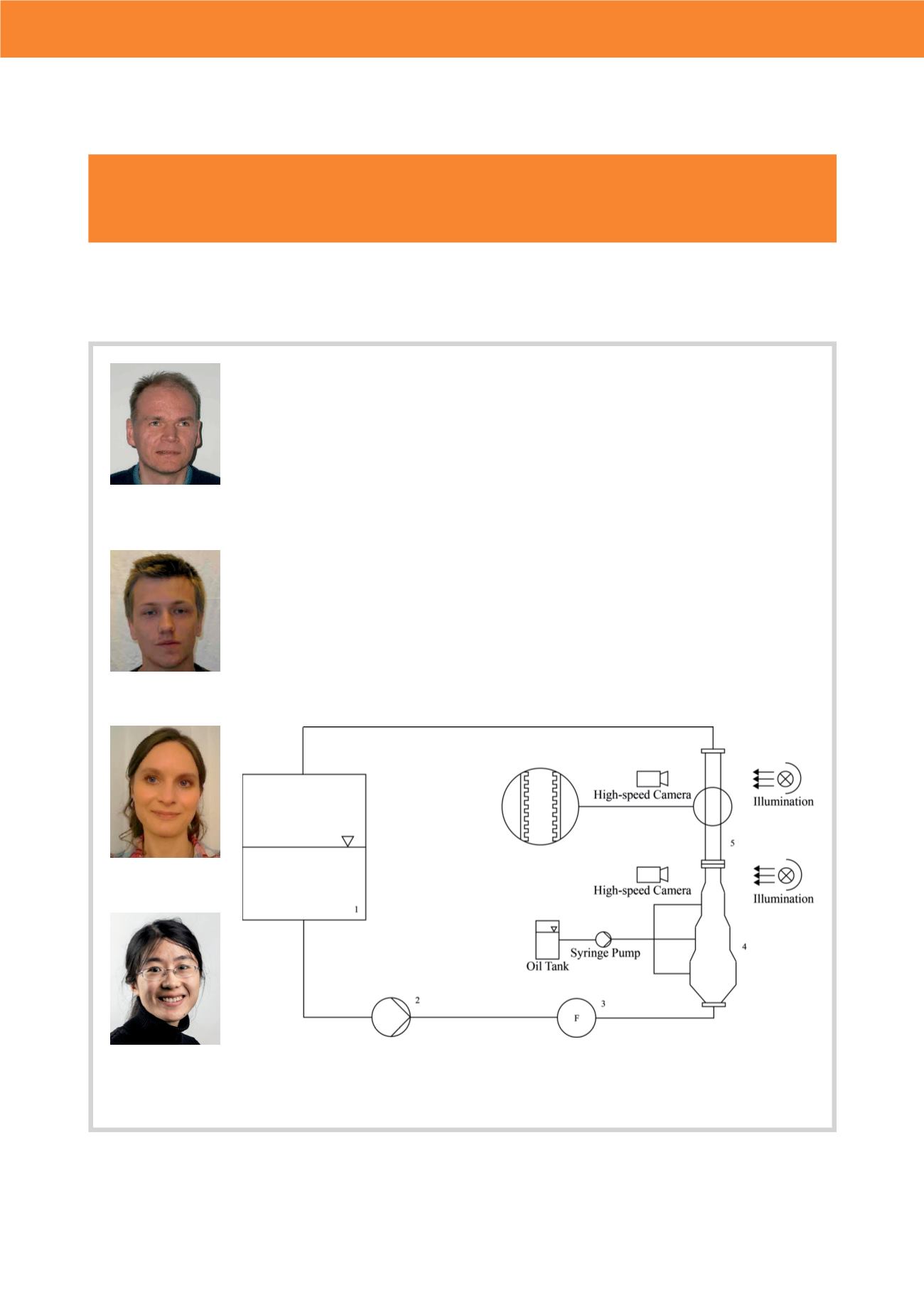
17
Annual Report 2015
A new regenerative process will allow production from wells with high H
2
S
concentration directly to transport line.
Experiments on fluid particle breakage and contactor studies
Project manager and
main PhD supervisor,
Prof. Hugo A. Jakobsen
PhD candidate,
Eirik Helno Herø
In order to facilitate subsea boosting and trans-
portation, phase separation of the hydrocarbon
flow subsea is often required. Phase separation
efficiency is severely dependent on the distribution
of the fluid particles size. The fluid particle size is
determined by equilibrium between various mech-
anisms of fluid particle breakage and coalescence
(particle merging). These mechanisms depend on
system properties, surface chemistry, operating
conditions, and flow phenomena. The current un-
derstanding and ability to predict these processes
is still immature and further research is needed.
In this project emphasis is placed on fundamen-
tal investigations of the fluid particle breakage
mechanisms.
A new experimental equipment for investigation
of single fluid particle breakage under controlled
flow conditions has been designed, based on a
literature survey, and is currently under construc-
tion. The novel part is the analysis section in which
more uniform turbulence dissipation rate level is
produced due to an enlarged wall roughness. It is
noted that only the drops moving in the centre part
of the tube will be considered to avoid wall effects
as the dissipation rate profile will have maxima
close to the walls. The experimental setup is
sketched in Figure 14.
The main aim is to perform experiments to
determine breakage frequency (breakage time
and breakage probability), number of daughter
particles created in breakage events, and size
distribution of daughter particles created in
breakage events.
Co-supervisor,
Dr. Jannike Solsvik
Postdoc, Jing Shi
of fluid particle breakage and coalescence (particle merging). These mechanisms depend on system
properties, surface chemistry, operating conditions, and flow phenomena. The current understanding
and ability to predict these processes is still immature and further research is needed. In this project
emphasis is placed on fundamental investigations of the fluid particle breakage mechanisms.
A new experimental equipment for investigation of single fluid particle breakage under controlled flow
conditions has been designed, based on a literature survey, and is currently under construction. The
novel part is the analysis section in which more uniform turbulence dissipation rate level is produced
due to an enlarged wall roughness. It is noted that only the drops moving in the centre part of the
tube will be considered to avoid wall effects as the dissipation rate profile will have maxima close to
the walls. The experimental setup is sketched in Figure 14.
Figure 14. Simplified flow diagram of the experimental set-up. 1) water/oil storage tank, 2) pump, 3)
flow meter/controller, 4) droplet generation section, 5) breakage analysis channel.
The main aim is to perform experiments to determine breakage frequency (breakage time and
breakage probability), number of daughter particles created in breakage events, and size distribution
of daughter particles created in breakage events.
Figure 14. Simplified flow diagram of the experimental set-up. 1) water/oil storage tank, 2) pump,
3) flow meter/controller, 4) droplet generation section, 5) breakage analysis channel.